Warning: Trying to access array offset on value of type bool in /var/www/foxof.com/wp-content/plugins/all-in-one-schemaorg-rich-snippets/functions.php on line 982
Warning: Trying to access array offset on value of type bool in /var/www/foxof.com/wp-content/plugins/all-in-one-schemaorg-rich-snippets/functions.php on line 982
Warning: Trying to access array offset on value of type bool in /var/www/foxof.com/wp-content/plugins/all-in-one-schemaorg-rich-snippets/functions.php on line 982
Warning: Trying to access array offset on value of type bool in /var/www/foxof.com/wp-content/plugins/all-in-one-schemaorg-rich-snippets/functions.php on line 984
Warning: Trying to access array offset on value of type bool in /var/www/foxof.com/wp-content/plugins/all-in-one-schemaorg-rich-snippets/functions.php on line 984
Warning: Trying to access array offset on value of type bool in /var/www/foxof.com/wp-content/plugins/all-in-one-schemaorg-rich-snippets/functions.php on line 984
How to choose an insulator taking into account all the parameters (performance, environment, installation, etc.)?
Share this page
Summary
- Introduction
- Choice criterion n°1: the constraints of the work
- Choice criterion n°2: the thermal properties of building materials and insulators
- Choice criterion n°3: the technical and environmental properties of the insulators
- Comparison of thermal performances of major insulating materials
- Comparative table of the insulators according to their performance and ecological aspects
- What to insulate first?
- Insulator qualitative reference point
- Compliance with thermal regulation
- Indicative prices
- Internal or external insulation?
- Rules of installing insulation
- Warning: moisture reduce the insulation performances
Heat loss of the construction by conduction
There are 3 modes of heat transmission: the convection, the radiation, the conduction. In the case of walls (walls, ceiling, floor), it is the phenomenon of heat conduction that describes the heat transfer between the interior and exterior (the hottest body – here the housing – transfers the energy to the coldest body – here the outside). The heat is “transfered” from the inside to the outside by moving from one material to another by contact. The role of the insulator is to limit this thermal transfer (summer as winter).

Thermal diagram of a poorly insulated wall
Choice criterion n°1: the constraints of the work
The insulation technique used (indoor, outdoor), the type of wall (walls, roof and attic, floors), the constraints of the work and the budget will determine the characteristics of the insulator to be chosen.
These construction choices will determine the processing of the insulator for each zone (bulk, rolls, plates, panels, flakes or aggregates, construction material, etc.) in order to facilitate its implementation and maximise its effectiveness.
When insulating from the inside, you can combine different types of insulators. However, it is necessary to ensure that the combination of the insulation retained has always a resistance to the diffusion of water vapour that decreases from the inside to the outside of the wall. Water vapour must never be blocked in the building or insulation itself.
Choice criterion n°2: the thermal properties of building materials and insulators
λ (W/m.K – Watt per meter Kelvin): Thermal conductivity of a material
- Low thermal conductivity materials are the best insulators. This value should be as low as possible. The best insulators have a coefficient λ = 0.007 W/m.K (while conventional insulators such as glass wool laine or expanded polystyrene λ = 0.04 W/m.K).
- The heat flow transmitted through the material depends on its thermal conductivity, thickness, surface and the difference in temperature between indoor and outdoor.
R (m².K/W): Thermal resistance of the insulators (applies to a single material)
- This corresponds to the “insulating ability” of a material of a given thickness.
- R = e/λ = thickness / thermal conductivity. An expanded polystyrene panel (λ = 0.032 W/m.K) of 10 cm will have an insulation ability of R = 0.1/0.032= 3.12 m².K/W.
- That’s the figure indicated on the packaging of the insulators. Higher the R is, the more efficient the wall is in terms of insulation. >> See the table of minimal regulatory values (later in this article).
U (W/m².K): Surface thermal transmission coefficient (applies to one multi-layer wall)
- It’s the amount of heat passing through one m2 of a heterogeneous (multi-layer) wall with a difference of 1°C between indoor and outdoor.
- Coefficient which defines the overall performance of the wall. This coefficient is the opposite of the thermal resistance (U=1/Rtotal_wall). Lower the U is, the more insulating the wall is.
- This coefficient is essential as it allows the calculation software to determine the actual losses (Watt) of a room. The overall thermal resistance of the wall (heterogeneous) is calculated, that is the sum of the resistances of each material composing the wall (ex.: drywall + glass wool + concrete + surface coating). For example Rtotal =0.24 m².K/W. For a difference of 15°C between the 2 sides of one wall (inside-outside) of 20m² we can calculate the loss. Loss (in W) = U (in W/m².K) x S (m²) x Δ (K) = (1/0.24) x 20 x 15 = 1250W. Therefore, a heater (or a heating system) capable of delivering that power is needed in the case of an outside temperature of 5°C and a desired room temperature of 20°C.
D (x 10-7 m²/s): Thermal diffusivity of an insulating material
- Characterises the capacity of a material to transfer more or less quickly the heat (from one wall to another). It reflects the inertia of the wall transmission (heat diffusion rate inside the material). The purpose is to slow the penetration of the external heat flow during the summer, and to limit the heat loss during the winter. The wood fibre has the lowest diffusivity, followed by the wood wool, OSB, aerated concrete. The higher the compression of the material (ex: rock wool 40kg/m³) the more the diffusivity is reduced.
E (J/m².s.°C): Specific thermal effusivity of an insulating material
- Characterises the rate at which the surface temperature of the material changes, i.e. the material’s capacity to exchange the energy more or less quickly with its environment. It plays the role of an internal atmosphere regulator.
- In the summer, in the event of large variations of heat, the concrete is the material (high effusivity) that best limits the heat input. It plays the role of a “thermal sponge” by limiting the heat input by day and by releasing the heat by night.
- In winter, the glass, hemp or sheep wools have a low effusivity, reflecting the fact that they are rapidly warmed at the surface (which helps to increase the temperature of the walls and thus to improve the apparent air temperature).
The control of thermal inertia reflects a combination of previous physical properties.
Choice criterion n°3: the technical and environmental properties of the insulators
The technical properties – non thermal – to be taken into account are:
- general water behaviour (degree of water absorption, dimension variation, performance degradation, behaviour in case of over-moisture, …),
- water vapour permeability: water vapour diffusion resistance coefficient (μ), or resistance factor of one material layer Sd = μ x d (m),
- air flow resistance (R=Pa.s/m2),
- mass density ρ (in kg/m3) to determine the inertia,
- volume heat capacity S (in kJ/m³.°C),
- incompressibility,
- stability and maintenance of performance over time,
- acoustic efficiency,
- burning behaviour,
- price and complexity of implementation.
Environmental properties of the insulators (environmental impacts):
- production energy = grey energy, transport, carbon balance,
- ability to be recycled,
- ability to be renewed,
- environmental and human toxicity, gas emissions, etc.
Regardless of the thermal, acoustic and technical performance, materials with the best eco-balance possible (natural, consuming low energy in the process of their manufacture-transport, renewable) should be used.
Comparison of thermal performance of the principal insulating materials

Photo Credit Insulation
The insulation is the first reduction source of energy needs of a building. The choice of a performant insulator and its installation ensure the continuity of the housing shell and the absence of thermal bridges. By choosing the insulating material, the aim is to maximise the comfort and to reduce the energy consumption by adopting a principle of bioclimatic design.
The wood fibre is ideal for slowing the heat flow of the lofts, roofs and walls exposed to the south. It’s also well-performing in terms of sound insulation. Strong compressive strength. High insulating performance, both in winter and in summer. Open to the diffusion of water vapour. Hygrometric regulator. Recyclable, ecological, environmentally friendly.
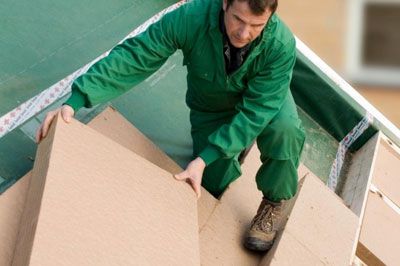
Photo Credit Steico
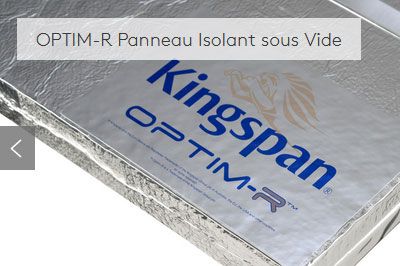
Photo Credit Kingspan
Some vacuum insulating panels combine exceptional thermal performances (λ = 0,007 W/m·K up to five times greater than other conventional insulating materials) and very low thickness for projects where every cm of space counts. The insulating panel is composed of a micro-porous core integrated into a thin sealed (vacuum) sheath (capsule). Delicate installation, cannot be drilled or cut.
The principle of bulk insulators (straw, hemp-lime, …) is to divide the insulating power over the entire thickness of the insulating layer. The principle is therefore completely different from traditional walls with multi-layer insulators, for which the insulating power is concentrated on a given layer. Their thermal performance is lower than that of the multi-layer insulators and the quality of the implementation of the mixtures is decisive.
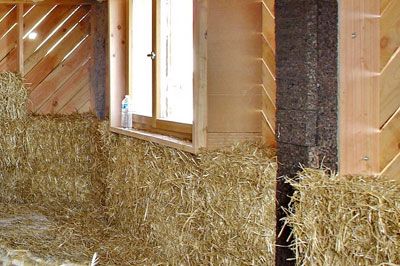
Photo Credit – RFCP: French Network of Straw Construction
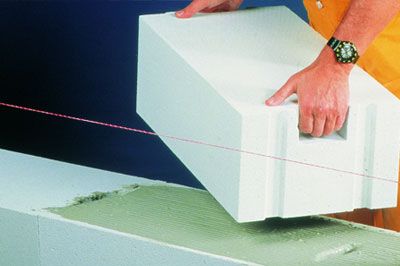
Photo Credit YTONG cellular concrete distributed insulation
For a more concrete comparative view of thermal efficiency (only the conductivity) of different insulators:
- 1 cm of qualitative vacuum insulator (ISOVIP type) represents 6-7 cm of expanded polystyrene (PSE) or 9-10 cm of mineral wool.
- For an R = 5 m².K/W it takes a thickness of 36 mm of a vacuum insulator (source – ISOVIP Saint Gobain) or 50 cm for a bulk insulator (but constructive) of cellular concrete!
Comparative table of insulators according to their performance and environmental aspects
The choice of the structure and its insulation must take into account the regulatory objectives of the thermal comfort both in summer and winter, while favouring environmentally friendly solutions.
Synthetic Insulator | |||
---|---|---|---|
Insulator |
Insulator Type | Main Advantages | Main Disadvantages |
Foams of polyurethane (PUR), extruded polystyrene (XPS), expanded polystyrene (PSE), polyisocyanurate (PIR) | Cellular Synthetic Insulator | Good thermal performance in winter (XPS). Easy installation (wall, ceiling, flat and inclined roof). | Made from non-renewable materials under energy consuming and environmentally destructive methods. The PSE is recyclable. Release of toxic and deadly gases in the event of combustion (fire). Poor acoustic performances. |
Resolic foams (or phenolic PF) | Synthetic Insulator | Very good thermal and phonic characteristics. Easy interior and exterior installation (wall, floor, ceiling, attic). Thickness gain = more net surface area. | Made from non-renewable materials under energy consuming methods. Price and moisture sensitivity. Possible impact on health and environment. Inflammable. |
Multi-layer reflective insulators (thin thermo reflective films, multi-layer films, PMR, …) | Synthetic insulator (aluminium, synthetic foams) | Low thickness. The reflective part send back the radiation (might be interesting for radiant heating mode). | Variable thermal characteristics. Inefficient to limit the heat flow by conduction and convection. No thermal inertia. Inefficient in attics. Search for certified products. To be used in addition with other insulators. Does not regulate hygrometry as it’s water vapour impermeable. Non renewable. Non recyclable. |
Vacuum insulating panels (VIP – Vacuum Insulation Panel) | Synthetic Insulator | Theoretically the vacuum insulation panels are the best insulators possible (= vacuum is the best insulator to stop heat). (λtheoretical = 0.004 W/m.K – λstaid = 0.008 W/m.K)
R = 6 m².K/W for only 30 mm! Performance 6 to 8 times greater than a mineral or animal wool. |
Search for products with certified performance. Complexity of installation (by accidental drilling it loses all its value = vacuum). No cuts possible. Handling the continuity between 2 panels (to avoid thermal bridges) is complex. Non water vapour permeable. High price (5 to 10 times the price of mineral wool). Non renewable. Non recyclable. |
Nanostructured materials from the future (aerogels,..) | Synthetic Insulator | The air (or the used gas) is trapped in nano-cells (small bubbles of one billionth of a meter) to prevent it from moving and conveying heat.
At the top of thermal and acoustic performance (λ = 0.011 W/m.K, 4 times more performant than vegetable or animal wool). Water vapour permeable, regulates hygrometry without stocking more than 1% of its weight in water. Non-hazardous to health! |
Manufacturing complexity resulting in a very significant cost to date. Non renewable. Non recyclable. |
Mineral Insulator | |||
---|---|---|---|
Insulator | Insulator Type | Main Advantages | Main disadvantages |
Mineral Insulators: volcanic rock wool (MW), glass wool (GW), mica, cellular glass (CG), perlite, vermiculite, expanded clay, … | Inorganic Insulator | MW and GW :
Price/Performance = correct. The most used to date. Good thermal and acoustic characteristics. Non inflammable. Rotproof. Does not absorb moisture. Reasonable ecological balance. Recyclable. |
Possible irritation (skin, respiratory tract, eyes) when installing. |
Vegetable Insulator | |||
---|---|---|---|
Insulator | Insulator Type | Main Advantages | Main disadvantages |
Vegetable Wool: wood fibre (WF), wood wool (WW) | Ecological Insulator | + Wood fibre/wood wool: Good thermal and acoustic performance both in summer and winter for a reasonable price. Choose the FSC, PEFC (sustainably managed forests), FDES (A or A+) labels. Very suitable for both internal and external insulation (including sarking). Hygrometric regulator if installed with vapour barrier. Recyclable, ecological, environmentally friendly. | + Wood fibre/wool: attention to additives: binder to ensure the rigidity (polyester, polyurethane, textile fibres or latex) + complementary fungicidal, insecticidal, fire-retardant treatments. Installation under good practice to avoid any moisture stagnation. |
Vegetable Wool: coconut fibre, hemp, cork, cotton, flax, straw, reed, grass wool, … | Ecological Insulator | + Coconut fibre: low grey energy but transport (Asia), no chemical addition necessary, safe for health and environment. Good thermal and excellent acoustic performance. Rotproof. Regulates moisture. Sustainability. + Cork: good thermal and acoustic characteristics (including inertia). Hardly inflammable. Rotproof. Renewable, recyclable, low grey energy consumer. Very stable over time.+ Cotton: good regulator of air hygrometry. Recyclable except for non-natural binders. Attractive price if recycled. |
+ Hemp: inflammable and moisture sensitive (except additives). Additive polyester for structuring. Price +15% / mineral wool.
+ Coconut fibre: high price. + Cork: high price. + Cotton: very polluting culture + transport. Requires a treatment against mould and insects. Combined with 15%-20% polyester. |
Cellulose: cellulose wadding, recycled paper or straw. | Ecological Insulator | Cellulose wadding: good thermal and acoustic characteristics. Brings a very good inertia (dephasing up to 10h). Good hygrometry regulator. Improve the air tightness of the casing. Limitation of thermal bridges (insufflation). Durability without loss of efficiency. Recyclable. Attractive price. | Additional treatments (antifungal, insecticidal, flame-retardant). Some technical constraints of the installation. |
Recycled textile fibre (cotton, synthetic textile, glass fibre) | Recyclable | Good thermal and phonic characteristics (depending on the nature of textiles of which it is composed). | Synthetic textiles and binders are a must to obtain the wooly structure (polyamide, polyester, acrylic) + additional treatments (antifungal, insecticidal, flame-retardant) |
The wood fibre is one of the most efficient materials for combating heat penetration in summer. Indeed, the wood has a large capacity to accumulate the heat (inertia) therefore to delay its penetration (dephasing of 12h in the attic for example). It is also very efficient in the winter to keep heat indoors. Wood fibre insulators regulate the hygrometry of the housing as the fibres are water vapour permeable.
Animal Insulator | |||
---|---|---|---|
Insulator | Insulator Type | Main Advantages | Main disadvantages |
Animal wool: sheep wool, duck feathers,. | (alias) Ecological Insulator | + Sheep wool: good thermal characteristics. Biodegradable, recyclable. Good regulation of ambient hygrometry.
+ Duck feathers: good thermal and acoustic characteristics. Good regulation of ambient hygrometry. Recyclable. Affordable price. |
Attention to necessary treatments (against the moths, fireproofing, moulds). Relatively high price. Transport (origin of the wool?).
Duck feathers: fire-sensitive. |
Insulator | Insulator Type | Main Advantages | Main disadvantages |
---|---|---|---|
Bulk Insulators (straw, concrete and lime-hemp mortar) | Recyclable Bulk Insulator | Very good regulation of ambient hygrometry but not to be placed in wet rooms. Very good phonic insulation. Good deal. | Lower thermal performance than traditional insulators, hence large thickness. |
Constructive Insulators (single wall brick, cellular concrete, terracotta, pumice stone, etc.) | Construction | + Cellular concrete: might avoid adding an additional insulation if the thickness of the blocks is significant (> 40 cm). Very good thermal inertia to avoid the heat penetration in summer (dephasing up to 13h) and heat losses in winter. Good acoustic insulation. Good hygrometry regulation. Does not require chemical treatments (rodents, insects). Non-flammable. Recyclable. Attractive price without additional insulation. | + Cellular concrete: significant grey energy. Average thermal conductivity λ = 0.1 W/m.K (offset by the thickness of the block). |
What to insulate first and foremost?
Rooms with at least one wall in direct contact with the outside. Unheated rooms (garage, cellar, laundry, etc.) in the case of regular occupancy. The thermal losses in an uninsulated housing indicate the priorities to be applied: roofing (25% to 30%), walls (20% to 25%), fresh air and leaks (20% to 25%), windows (10% to 15%), floor (7% to 10%), thermal bridges (5 to 10%). Source ADEME.
In the frame of a renovation, it is illusory to think that the over-insulation of one wall, will compensate for the absence or the insulation imperfections of another wall. Since the treatment of thermal bridges is essential in terms of insulation, each wall in contact with a non-heated area must be treated.
Diagnosis of the existing situation
There are 2 ways to know the performance of the housing in terms of thermal losses (therefore insulation performance):
- The EPC (Energy Performance Certificate) or EPD (Energy Performance Diagnosis). This mandatory document in a real estate sale is based on a calculation that takes into account the history of previous consumption (invoices and user lifestyle).
- The thermal audit is carried out by an engineering office. This is a real site-based study that determines the thermal losses, the localised thermal bridges, etc.
Qualitative benchmarks for insulators
Insulator laboratory certifications
Each mark of heat insulators offers different ranges and therefore different performance.
To choose a suitable insulation, choose a product whose values are certified (and not declarative!) by an independent body which respects the minimum values of the current thermal regulation.
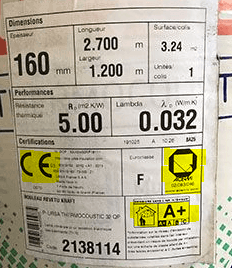
Labels and certification elements:
- CE Marking (compliance with European Construction Products Directive + is the subject of the Declaration Of Performance (DoP) according to the regulation of construction products).
- ECO-labels (natural materials and materials requiring only few resources in their production – grey energy): FSC, PEFC, BLUE ANGEL, etc.
- Environmental Impact: consult the sheets of the Environmental and Health Declarations (FDE&S) through the website INIES.
If the insulator does not enter the framework of an existing certification (e.g. innovative character), it might be subject of an UTD (unified technical document) or at least of a technical opinion of the BRE (British Research Establishment).
Thermal resistance of the insulator and the compliance of thermal regulation
Following an EPC (energy performance certificate) recommendations regarding insulation can be made. In order to choose well the insulation materials (depending on their performance) it is important to refer to the current thermal building regulation.
The current thermal regulations for the work in existing buildings set the minimum performance of the insulation through the thermal resistance coefficient R of the insulation. When insulation works are carried out in an existing building, the minimum performance requirements in terms of insulation are:
- R (m².K/W) ≥ 6 for attics or crawling roofs
- R ≥ 7 for the floor of an unused attic
- R ≥ 3 for the floor (above a basement, crawl space or open passage)
- R ≥ 4,5 for flat roofs
- R ≥ 4 for walls (external and internal – facade or gable)
In new construction, the current thermal regulation imposes the minimum performance values as follows:
- R (m².K/W) ≥ 8 for the roof (crawling roofs and ceiling of attics)
- R ≥ 4 for walls (facade or gable)
- R ≥ 4 for floors (on the ground).
These performances are very demanding and involve significant thickness of the insulation (sometimes 30cm) that are not possible in renovation (except for an external insulation).
Tariff benchmarks relating to insulators
Eligible households can apply for a grant to install insulation using a Registered Insulation Installer. The ‘Big Six’ utility companies, including Npower, EDF and British Gas, are obliged to provide funding so that those who need to can improve the efficiency of their homes.
Floor insulation:
- Example: R=4.2 m².K/W: insulation by 17 cm of cellulose wadding of thermal resistance λ = 0.040W/m.K. Material budget: £60/m2
- Example: R=0.75 m².K/W: thermal and phonic insulation under screed or massive slab by 3 cm of wood fibre board of thermal resistance λ = 0.038W/m.K. Material budget: £6/m2
Insulation of walls:
- Example: R=7 m².K/W: 37 cm insulation of straw bales (clay coated). Material budget: £10€/m2
- Example: R=3.85 m².K/W: 14 cm insulation of cellular glass panel. Material budget: £10/m2
- Example: R=5 m².K/W: 20 cm insulation of hemp+flax+cotton mixed panel. Material budget: £25/m2
- Example: R=4 m².K/W: 3.6 cm insulation of ISOVER vacuum insulation panel. Material budget: £200/m2
- Example: wall phonic insulation of 4 cm panels made of corkcoco (cork + coconut fibre). Material budget: £30/m2
External insulation:
- Average rates: £100€/m2
Internal, mixed or external insulation?
With comparable insulation performance, external insulation has several advantages in comparison to the internal insulation:
- The treatment of thermal bridges (changes in plans or walls, junctions, elements of structure) is more efficient which limits heat losses.
- The risk of internal condensation of the insulator is limited. The external coating of the insulator must be vapour permeable and runoff waterproof. The moisture penetrates less inside the wall.
- Improves thermal inertia (its capacity to accumulate heat).
- Does not reduce the habitable surface.
- These advantages are also valid for thermal insulation of the roof by the outside (ITTE) – the so called sarking technique.
The insulation is covered with a coating or a cladding protecting the insulation but must remain “breathable” in order to let the moisture pass from the inside to the outside.
The mixed insulation consists of using construction materials for the structure which is both bearing and insulating. That’s the case of cellular concrete or terracotta. Additional insulation is usually provided either inside or outside, if the constructive blocks have a thickness of less than 30 cm.
Learn more about the latest innovations for covered outdoor and garden
Rules of laying down the insulation
The installation of the selected insulation must be carried out according to good practice of the profession. Indeed, the insulation elements (and vapour barriers) must be perfectly connected between them to avoid hot air leakage (air tightness). The holes for the passage of duct and cables must be accurately plugged as they represent up to 38% of leak tightness defects. The installation of a suitable vapour barrier is therefore an essential point that contributes to both air tightness and regulation of water vapour (to avoid condensation).
Warning: moisture reduces the performance of the insulation
Therefore, it is essential to remove excess moisture produced by the housing, using an efficient ventilation (permanent if possible).
Controlling the water vapour transfer through the walls is a key element in an indoor insulation project. Moreover, the successive layers of materials constituting the wall must be increasingly permeable to water vapour as it gets closer to the outside of the wall.
The installation of a vapour barrier or vapour retarder (on the inside wall just prior to the finish facing) limits the risks of condensation inside the wall. The vapour barrier blocks the entry of the vapour in the wall. The vapour retarder allows to regulate heat transfer (by lowering the pressure) while allowing the wall to breath (« breathing » walls). There are also “smart” membranes that are more or less permeable depending on the ambient moisture. This additional element does not exclude an efficient and permanent ventilation to remove moisture contained in the air (breathing, kitchen, shower, etc.). The higher the Sd value is, the less the product let the water vapour pass through.
On the outside, in order to avoid the penetration of rainwater into the exposed facades, a runoff impermeable coating (or any equivalent material) is essential.
Moisture lowers significantly the performance of the insulating material (water is thermally conductive). Therefore, abnormal moisture sources (leak tightness, infiltrations) should be removed to maintain good insulation performance.
During the winter, it is warmer and there is more moisture inside than outside. The water vapour tends to escape towards the outside. If it meets cold elements (as a result of thermal bridges in the wall), it tends to condensate (pass to the liquid state) which – over time – will cause mould (on the surface and/or inside).
To know more about identification of thermal bridges and mould risks
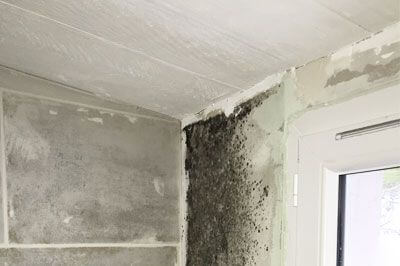
FOX45

